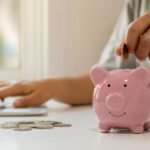
Here’s How to Start an Amazon FBA Business with Little Money
31 January 2024
Fix Amazon Image Mix-Up If Picture Does Not Match Product
31 January 2024Welcome to the Ultimate Guide to FBA Barcode Requirements! If you’re a seller on Amazon’s FBA platform, it’s crucial to understand the barcode requirements to ensure smooth fulfillment and avoid penalties or fees.
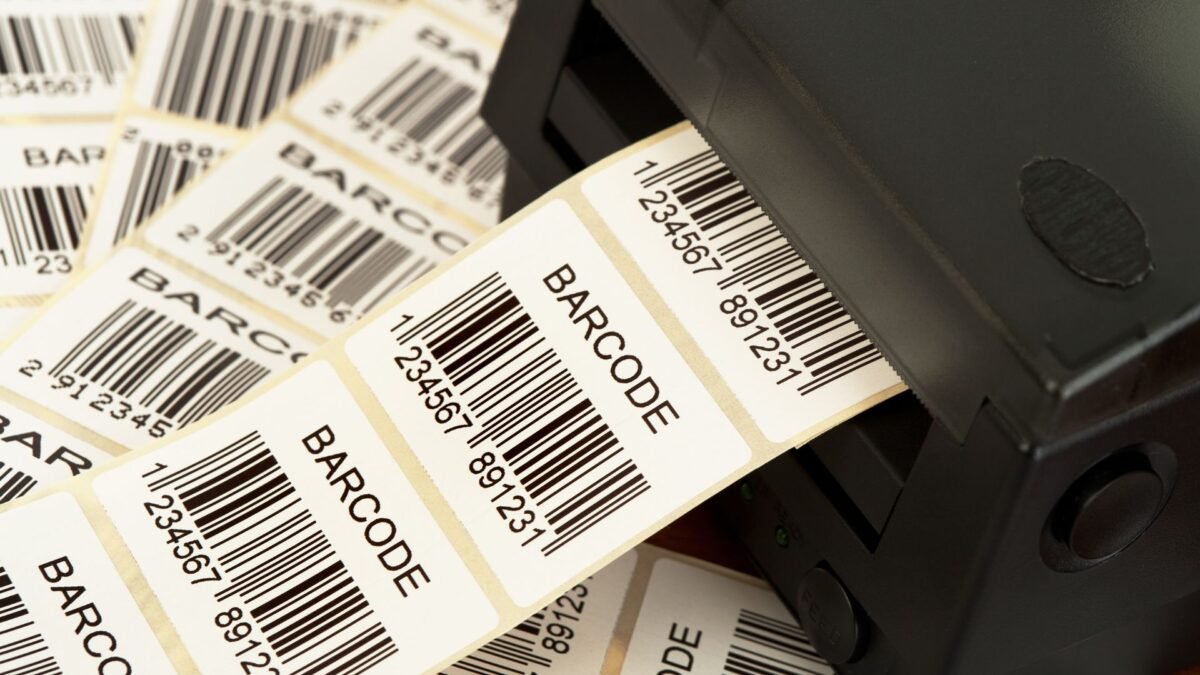
In this comprehensive guide, we will cover everything you need to know about packaging, labeling, and barcode types for selling on Amazon.
So let’s dive in and get you up to speed!
Key Takeaways:
- Understanding FBA barcode requirements is essential for successful selling on Amazon.
- Amazon accepts three main types of packaging: box packs, poly bags, and blister packs.
- Packaging must meet specific requirements, including dimensions, durability, and suffocation warnings.
- Every unit sent to Amazon through FBA must have a barcode, preferably the FNSKU barcode for private label products.
- Labels should be placed correctly and cover any other visible barcodes to avoid labeling mistakes.
Packaging Types for Amazon FBA
When it comes to fulfilling orders through Amazon’s FBA program, choosing the right packaging is crucial.
Amazon accepts three main types of packaging: box packs, poly bags, and blister packs.
Each packaging option serves different purposes and offers unique advantages, allowing you to choose the one that best suits your product’s needs and requirements.
If your product requires sturdy protection or a custom presentation, box packs are the way to go.
You can opt for a custom-designed box or a plain cardboard box that securely holds your product. This packaging type ensures that your product arrives safely at its destination while also providing a professional and polished appearance.
On the other hand, if your product doesn’t require a box or benefits from being easily visible, poly bags are a suitable choice.
Poly bags are lightweight, cost-effective, and ideal for products that don’t need the extra protection of a box.
They are particularly useful for items like clothing, accessories, or small lightweight products that can be easily sealed in a transparent bag.
Finally, blister packs are a packaging option for products that benefit from displaying their contents.
Blister packs consist of a transparent plastic cavity that holds the product, allowing customers to see the item before making a purchase.
This packaging type is commonly used for electronics, toys, or small items that can be easily showcased through the packaging.
It’s important to note that regardless of the packaging type you choose, all units must be fully contained within the packaging to meet Amazon’s FBA requirements.
This ensures that your product is effectively protected and ready for shipment.
Packaging Type | Advantages |
---|---|
Box Packs |
|
Poly Bags |
|
Blister Packs |
|
Requirements for Boxed Units
Boxed units play a crucial role in maintaining the integrity of your products during the fulfillment process.
To ensure that your boxed units are accepted by Amazon, it’s important to meet their specific requirements.
By doing so, you can streamline your operations and avoid any potential issues that may arise.
Box Dimensions
When packaging your products, it’s essential that the box dimensions meet Amazon’s guidelines.
The box should be six-sided and properly sealed with openings or a lid that securely closes.
This helps to protect your products from any damage during storage and transportation.
Strength and Durability
Amazon requires that the box withstand medium force without breaking.
This ensures that your products remain protected throughout their journey in the fulfillment center and during shipment to customers.
It’s important to choose a sturdy and durable box that can withstand handling and potential impacts.
Drop Test
In addition to the strength and durability of the box, Amazon also requires that boxed units pass a three-foot drop test.
This test evaluates the box’s ability to protect the contents in case of accidental drops during handling and transport.
If the box fails the drop test, the product must be placed in a poly bag along with a suffocation warning.
Meeting Amazon’s requirements for boxed units is crucial for a successful fulfillment process.
By ensuring that your boxes are properly sized, strong, and pass the drop test, you can provide a positive customer experience while avoiding any penalties or issues with your Amazon FBA shipments.
Requirements for Poly Bagged Units
If you choose to package your product in a poly bag, it’s crucial to comply with Amazon’s FBA poly bag requirements.
These guidelines ensure the safety of your product during shipping and handling, as well as compliance with relevant regulations.
To meet Amazon’s requirements, your poly bag must adhere to the following specifications:
- The poly bag must have an opening of at least five inches.
- The bag should be transparent, allowing for easy visibility of the product inside.
- The bag should have a thickness of at least 1.5 mil to provide proper protection.
- The barcode (UPC or FNSKU) must be placed in a scannable location on the bag.
- The poly bag must be completely sealed to prevent any damage or tampering.
- The dimensions of the poly bag should not exceed the dimensions of the product by more than three inches in any direction.
In addition to these requirements, a suffocation warning label must be included on the poly bag if the opening exceeds a certain size.
This warning serves as a precautionary measure to prevent accidental suffocation, especially for small children.
Here is an example of how the suffocation warning label should be displayed:
Requirement | Description |
---|---|
Poly Bag Opening Size | At least five inches |
Transparency | Transparent |
Thickness | At least 1.5 mil |
Barcode Placement | Scannable location on the bag |
Sealing | Completely sealed |
Size Limit | Does not exceed product dimensions by more than three inches |
By adhering to these requirements, you can ensure that your poly bagged units are in compliance with Amazon’s guidelines and regulations, promoting a safe and efficient fulfillment process.
Packaging Mistakes to Avoid
When it comes to selling products on Amazon through FBA, avoiding packaging mistakes is crucial. Packaging errors can lead to additional fees and penalties, which can impact your profitability.
To ensure a smooth fulfillment process and maximize customer satisfaction, keep these packaging guidelines in mind:
Contain All Product Pieces in One Package
- Make sure that all the components or pieces of your product are contained within one package. This ensures that nothing gets lost during the fulfillment process and that customers receive all the necessary items.
Adhere to Size Constraints
- Follow Amazon’s size constraints for the standard size tier. The overall dimensions of your packaging should be within the specified limits to avoid any additional fees. Be aware of the acceptable weight and size limits for your product category.
To help you understand the packaging mistakes to avoid, take a look at the table below:
Packaging Mistake | Consequences |
---|---|
Missing or incomplete product pieces | Unsatisfied customers, negative reviews |
Oversized packaging | Additional fees, restrictions in storage and transportation |
Undersized packaging | Potential damage during fulfillment and transportation |
Inadequate protection | Product damage, returns, and customer complaints |
By avoiding these common packaging mistakes, you can minimize the risk of issues and ensure a seamless fulfillment process.
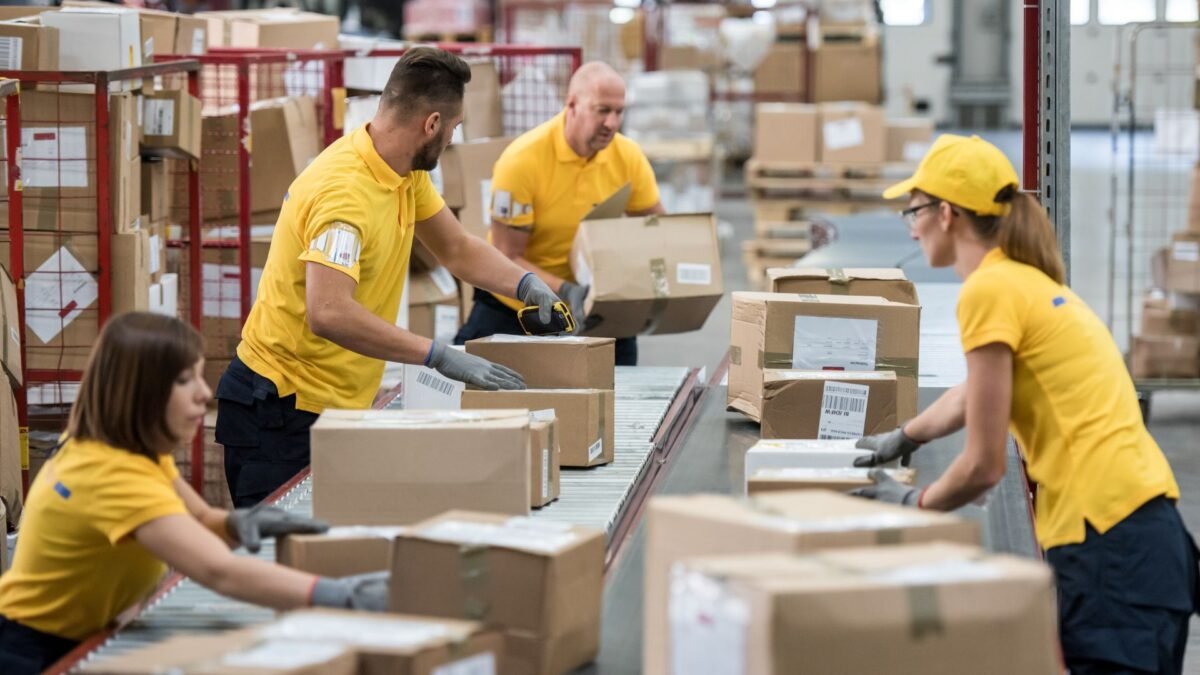
Taking the time to carefully package your products according to Amazon’s guidelines will not only help you avoid penalties but also enhance your brand’s reputation and customer satisfaction.
FBA Barcode Requirements
Every unit sent to Amazon through FBA must have a barcode. For private label products, it is recommended to use the FNSKU barcode instead of the UPC barcode.
The FNSKU can be obtained from the manage inventory page or while creating a shipping plan. It must be printed on the outermost packaging, and there should be only one visible barcode.
If there are other barcodes visible, they should be covered with a sticker.
Why FBA Barcode Requirements are Important
FBA barcode requirements are crucial because they ensure accurate tracking and identification of your products within Amazon’s fulfillment centers.
By adhering to these requirements, you provide a seamless experience for customers, prevent inventory mix-ups, and enable efficient fulfillment and inventory management.
Benefits of Using FNSKU Barcode
The FNSKU barcode is a unique identifier assigned to each product in Amazon’s fulfillment network. Using the FNSKU barcode for private label products offers several benefits:
- Ensures accurate tracking and inventory management
- Reduces the risk of product misidentification
- Provides better control and visibility over your inventory
- Prevents commingling of your products with other sellers’ products
By using the FNSKU barcode, you have greater control over your brand and product listings, improving your overall selling experience on Amazon.
Printing and Labeling Guidelines
To comply with FBA barcode requirements, follow these guidelines for printing and labeling:
- Obtain the FNSKU barcode from the manage inventory page or while creating a shipping plan.
- Print the FNSKU barcode on the outermost packaging of each unit.
- Ensure there is only one visible barcode, which should be the FNSKU barcode.
- If there are other barcodes visible on the packaging, cover them with a sticker.
Following these guidelines will help you meet FBA barcode requirements and ensure smooth fulfillment and accurate tracking of your products on Amazon.
How to Print FNSKU Barcode
Printing FNSKU barcode is a crucial step in ensuring your Amazon FBA products are properly labeled and ready for fulfillment.
Here’s a step-by-step guide on how to print the FNSKU barcode:
- Step 1: Access the manage inventory page or the shipping plan creation process on Amazon Seller Central.
- Step 2: Locate the FNSKU barcode for the specific product you’re preparing for shipping.
- Step 3: Print the FNSKU barcode as a PDF file.
- Step 4: Send the PDF file containing the FNSKU label to your supplier.
- Step 5: Instruct your supplier to apply the FNSKU label to each unit’s outermost packaging.
- Step 6: Ensure the FNSKU label is placed prominently and is easily scannable by Amazon.
- Step 7: If necessary, consider incorporating the FNSKU barcode into your package design or using a sticker to maintain a clean and professional appearance.
By following these straightforward steps, you can ensure your products are properly labeled with the FNSKU barcode, meeting Amazon’s requirements for FBA fulfillment.
Example of FNSKU Barcode Label Placement:
Package Type | Label Placement |
---|---|
Boxed Units | Apply the FNSKU barcode label on the outermost packaging of each unit. |
Poly Bagged Units | Attach the FNSKU barcode label to the transparent poly bag in a scannable location. |
Custom Package Design | Incorporate the FNSKU barcode into the design or use a sticker prominently placed on the package. |
Ensuring accurate and visible FNSKU barcode label placement is essential to expedite the fulfillment process and avoid any potential issues with the scanning and tracking of your products.
Labeling Tips for FBA Products
When it comes to labeling your FBA products, here are some tips to ensure a smooth and efficient process.
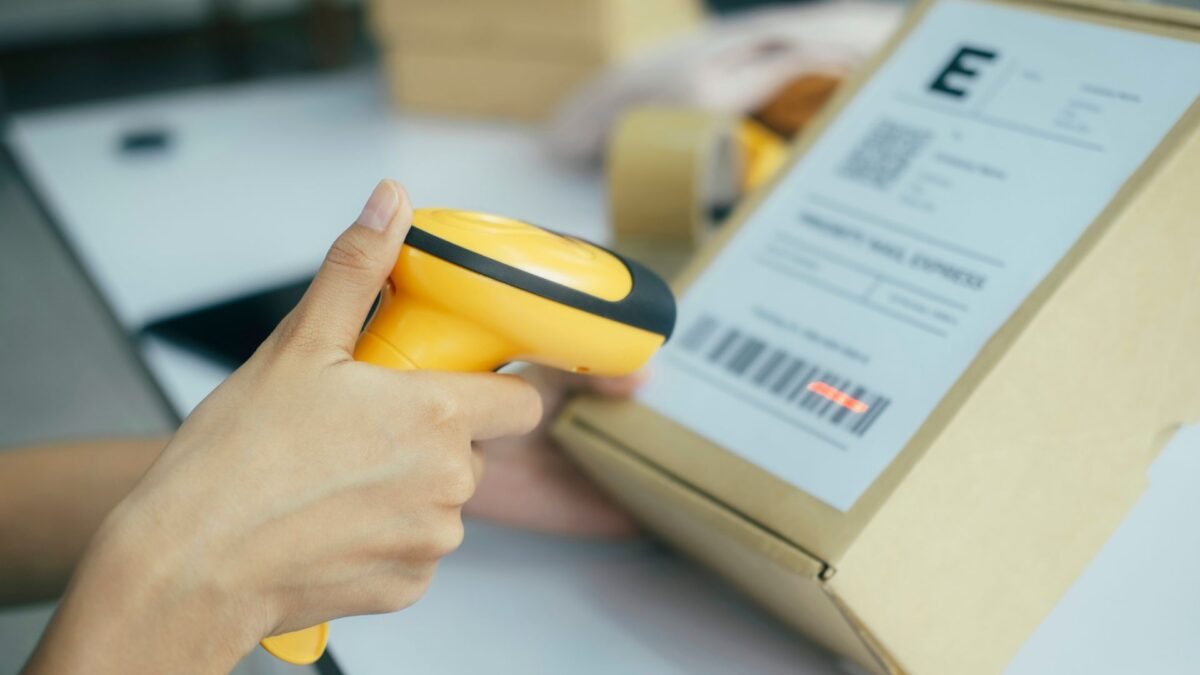
Whether you have a custom package design or are using stickers, these tips will help you meet the FBA labeling requirements and enhance the presentation of your products.
1. Incorporate FNSKU and Country of Origin on the Box
If you have a custom package design, consider incorporating the FNSKU barcode and the country of origin directly onto the box.
This not only ensures that the necessary labeling information is clearly visible but also adds a professional touch to your packaging. Customers will appreciate the attention to detail and transparency.
2. Combine FNSKU and Country of Origin on a Single Sticker
If you prefer to use stickers for labeling, optimize space and reduce costs by combining the FNSKU barcode and the country of origin on one sticker.
This simple yet effective approach keeps the packaging tidy and minimizes the chances of other visible barcodes causing confusion during scanning.
3. Ensure Correct Label Placement
Proper label placement is essential for accurate scanning and inventory identification. Make sure the FNSKU label is positioned correctly on the outermost packaging of each unit.
It should be easily visible, scannable, and not obstructed by any other elements or barcodes. Maintaining label integrity is crucial for efficient fulfillment and inventory management.
4. Cover Other Visible Barcodes with Stickers
To comply with FBA requirements, it’s important to cover any other visible barcodes on your packaging. Utilize stickers or labels to ensure only the FNSKU barcode is visible.
This prevents confusion during the scanning process and ensures accurate tracking of your products.
By following these FBA labeling tips, you can streamline your operations, improve product visibility, and enhance the overall customer experience.
Remember to always double-check the accuracy and placement of your labels to avoid any issues with fulfillment and inventory management.
FBA Labeling Tips: |
---|
Incorporate FNSKU and country of origin on the box |
Combine FNSKU and country of origin on a single sticker |
Ensure correct label placement |
Cover other visible barcodes with stickers |
Labeling Mistakes to Avoid
When it comes to selling on Amazon, correct labeling is vital to ensure smooth operations and avoid unplanned service fees.
Abiding by Amazon’s FBA labeling guidelines is crucial to maintain compliance and prevent unnecessary penalties. Here are some common labeling mistakes to avoid:
- Missing labels: Failure to include the necessary labels on your products can lead to complications. Make sure that every unit has the required labeling, including any specific requirements such as expiration dates.
- Incorrect labels: Using the wrong type of label or not following Amazon’s labeling specifications can result in non-compliant products. It’s essential to understand the guidelines and use the correct label type for each item.
- Illegible labels: Labels that are blurry, smudged, or difficult to read can cause delays in processing and ultimately result in customer dissatisfaction. Ensure that your labels are clearly printed and easily scannable by Amazon.
By avoiding these labeling mistakes, you can save yourself from unplanned service fees and maintain a smooth fulfillment process. Always double-check your labeling to ensure compliance with Amazon’s guidelines.
Example Labeling Mistake:
Labeling Mistake | Consequences |
---|---|
Missing expiration date label | Risk of selling expired products |
Using an incorrect barcode format | Difficulty in scanning and processing |
Smudged barcode label | Delays in processing and shipping |
Ensuring accurate and compliant labeling is crucial for a successful Amazon FBA business. Take the time to familiarize yourself with Amazon’s labeling guidelines and implement proper labeling practices from the start.
Carton Requirements for Shipping
When shipping products to Amazon, it’s important to meet the carton requirements to ensure smooth transportation and delivery.
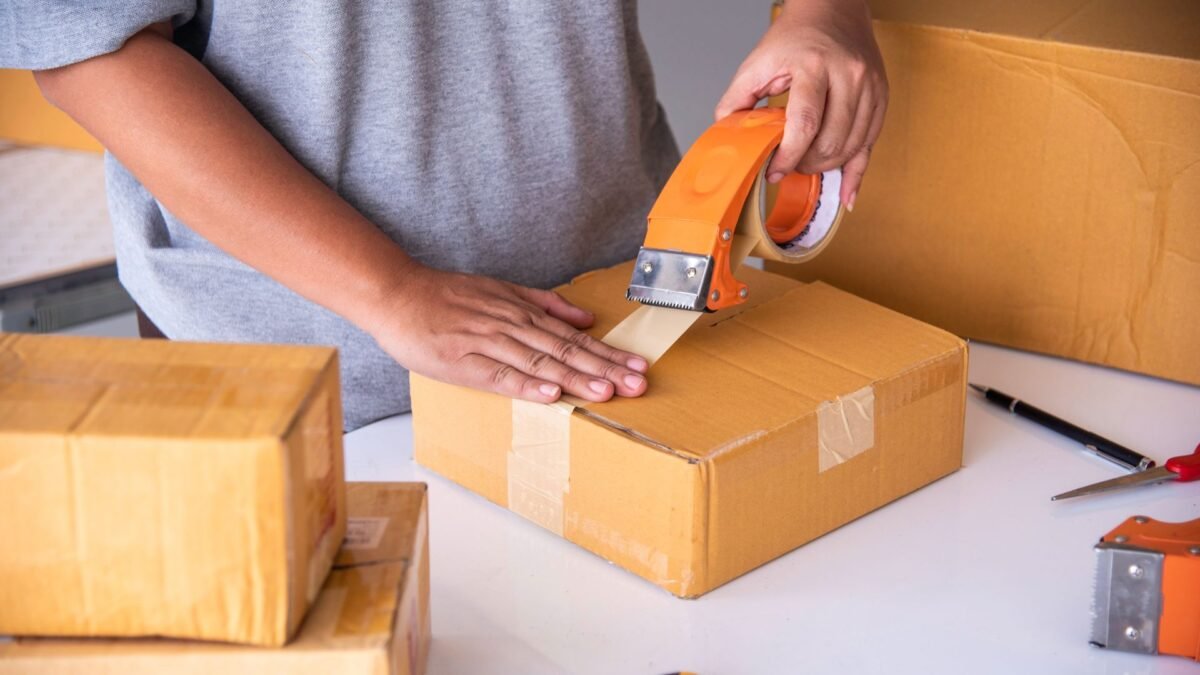
By adhering to these guidelines, you can avoid any delays or complications that may arise during the shipping process.
Shipping Carton Dimensions
The dimensions of your shipping cartons play a crucial role in determining how efficiently your products can be handled and transported. To comply with Amazon’s carton requirements, follow these guidelines:
- The cartons should not weigh more than 50 pounds
- The cartons should not exceed 25 inches on any side
By adhering to these weight and size limits, you can ensure that your cartons can be easily managed and transported by Amazon’s logistics network.
Partnered Carrier Shipments
For partnered carrier shipments, there is a maximum limit of 200 units per carton. Partnered carrier shipments offer several advantages, including discounted shipping rates through Amazon’s program.
Adhering to the maximum limit can help you optimize your shipping costs and streamline your supply chain.
Non-Partnered Carrier Shipments
For non-partnered carrier shipments, the maximum limit is 500 units per carton.
While non-partnered carrier shipments do not offer the same cost-saving benefits as partnered carrier shipments, they still provide a reliable option for shipping your products to Amazon.
To ensure successful delivery, it’s important to carefully pack and label your cartons according to Amazon’s guidelines.
This includes labeling each carton with the necessary shipping labels and ensuring that they are applied securely and clearly visible.
Following Amazon’s carton requirements will help you maintain a smooth shipping process, prevent any delays or complications, and ensure timely fulfillment of your products.
By meeting these requirements, you can create a positive customer experience and enhance your overall business performance on Amazon.
Shipping Labels Requirement
Accurate labeling of your shipping cartons is crucial to ensure smooth processing of your inventory on Amazon. It is a requirement set by Amazon to apply shipping labels to each carton you send.
This helps Amazon to identify and route your products correctly for fulfillment. To meet this requirement, you have a few options:
Option 1: Amazon Labels
If you prefer convenience, you can choose to have Amazon label your products for a fee.
During the shipping plan process, Amazon provides shipping labels that are specific to the fulfillment centers your products will be shipped to. You can opt for this service and let Amazon handle the labeling on your behalf.
Option 2: Self-Labeling
If you prefer to label the units yourself, you can do so by generating the shipping labels provided by Amazon.
These labels contain important information, such as the fulfillment center address, shipping box ID, and barcode. Make sure the labels are printed clearly and adhere them securely to each carton.
This ensures that your packages are easily scannable by Amazon’s systems during the receiving process.
Additionally, when shipping your products, you will also need to affix the shipping carrier labels to each carton.
These labels are generated by your supplier or freight forwarder and contain information such as the shipping address, tracking number, and carrier logo.
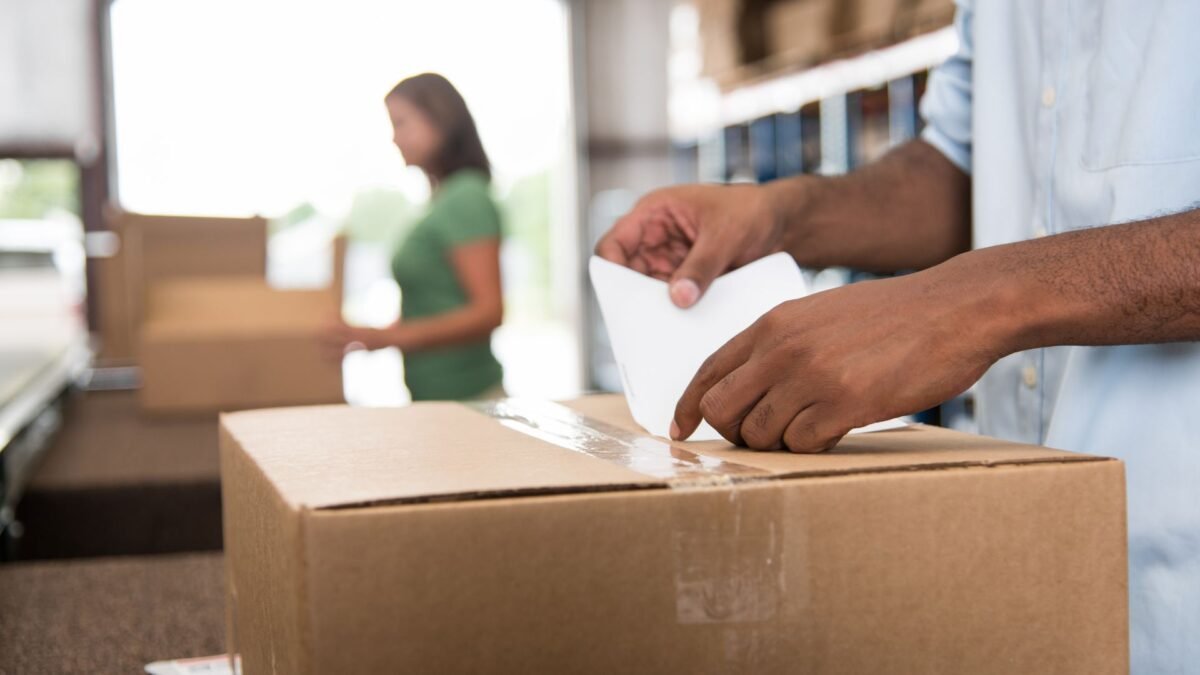
By ensuring that your shipping labels are applied correctly and legible, you can help minimize delays and improve the efficiency of your inventory processing.
Shipping Labels Options | Pros | Cons |
---|---|---|
Amazon Labels | – Convenient and time-saving – Professionally generated and applied – Ensures compliance with Amazon’s labeling requirements | – Additional fee – May not have full control over label placement |
Self-Labeling | – Cost-effective – Enables control over label placement – Can use preferred label printers | – Requires time and resources – Must ensure accurate label printing and placement |
Frequently Asked Questions
Finished going through our helpful guide on FBA barcode requirements? If you’re left with more questions, don’t worry, we’ve got you covered down below.
What are some packaging mistakes to avoid?
To avoid additional fees and penalties, make sure all product pieces are contained within one package and that the overall size of the packaging doesn’t exceed the size constraints for the standard size tier.
Do I need a barcode for every unit sent to Amazon through FBA?
Yes, every unit sent to Amazon through FBA must have a barcode, preferably the FNSKU barcode for private label products.
How do I print the FNSKU barcode?
You can obtain the FNSKU barcode from the manage inventory page or while creating a shipping plan, save it as a PDF, and send it to your supplier to be applied to each unit.
What labeling mistakes should I avoid?
Incorrectly labeled or missing labels can result in unplanned service fees. Make sure to correctly label your products, including any specific requirements such as expiration dates, and follow Amazon’s labeling guidelines.
Do I need shipping labels for my products?
Yes, Amazon requires shipping labels to be applied to each shipping carton. They provide shipping labels through the shipping plan process, and you can choose to have Amazon label your products for a fee or label them yourself.
What is the importance of following FBA barcode requirements?
Following FBA barcode requirements is essential for smooth fulfillment and can help you avoid penalties or fees. It ensures accurate processing of your inventory and provides a seamless experience for your customers.
Conclusion
Properly understanding and following FBA barcode requirements is essential for a successful business on Amazon.
From packaging to labeling and barcode types, each step plays a crucial role in ensuring smooth fulfillment and avoiding penalties or fees.
By adhering to these requirements, you can maximize your chances of success and provide a seamless experience for your customers.
Amazon’s FBA barcode requirements cover various aspects of your product’s journey, including packaging, labeling, and barcode types.
Packaging should be chosen carefully, ensuring it provides adequate protection for your product. Whether you opt for box packs, poly bags, or blister packs, make sure it meets Amazon’s standards.
For boxed units, the dimensions should be six-sided, securely closed, and able to withstand medium force and the three-foot drop test.
Poly bagged units need to have a suffocation warning label if the bag has an opening of at least five inches. The bag itself should be transparent, of sufficient thickness, and sealed properly.
Remember to place the barcode in a scannable location. When it comes to labeling, each unit sent to Amazon through FBA requires a barcode.
Consider using the FNSKU barcode, obtained from the manage inventory page or during the shipping plan creation process. Ensure that only one visible barcode is present and any other barcodes are covered.